Modelling the Effects of Mechanical Stress for Batteries in Wearable Applications
Create and release your Profile on Zintellect – Postdoctoral applicants must create an account and complete a profile in the on-line application system. Please note: your resume/CV may not exceed 2 pages.
Complete your application – Enter the rest of the information required for the IC Postdoc Program Research Opportunity. The application itself contains detailed instructions for each one of these components: availability, citizenship, transcripts, dissertation abstract, publication and presentation plan, and information about your Research Advisor co-applicant.
Additional information about the IC Postdoctoral Research Fellowship Program is available on the program website located at: https://orise.orau.gov/icpostdoc/index.html.
If you have questions, send an email to ICPostdoc@orau.org. Please include the reference code for this opportunity in your email.
Research Topic Description, including Problem Statement:
Wearable technologies are becoming an increasingly large industry. As of 2017 the global wearables market was worth ~$38 Billion by revenue and is forecasted to reach ~$85 Billion by 20221. A breakdown of the market shows that smartwatches, fitness trackers and medical devices dominate the industry. There is also significant growth expected in the e-textile market, from an almost non-existent market in 2016 to ~$2 Billion by 20222. This has been driven by the miniaturization and reduction in power consumption of electronics, advances in the maturity of printed electronics and developments in weaving conductive threads. To further battery technology in these sectors, it is anticipated that batteries will be embedded directly into garments.
The impact of the natural movement of a human and their garment on the mechanical stresses that develop within a lithium polymer cell is not well understood. As such, embedded batteries in a wearable device are typically limited to a coin cell or a lithium ion cell, which is encased in a relatively rigid outer packaging. Utilizing lithium polymer cells, which are not rigidly encased and are instead in mechanically conformable devices will increase consumer appeal and could enable advanced power systems for wearables and e-textiles products.
The aim of this topic is to better understand the mechanical and electrical degradation of lithium polymer cells under a variety of mechanical stresses typical to wearable applications.
There is open source information on the biomechanical movements and the muscular and joint forces of the shoulder region3 and the lower body during exercise4. Several e-textile and wearable porotypes have been evaluated in the literature5, where serpentine printed structures or woven conductors are used to aid strain relief during natural garment movement.
These studies suggest that the number of mechanical variables that wearable electronics, specifically lithium polymer cells in this scenario, may undergo is vast. For example, the bending radii, number of bending cycles, twisting angle, effect of ‘scrunching’, the dimensions and aspect ratio of the lithium polymer cell, and the effect of the substrate or material supporting the lithium polymer cell (for example fabric, polymer, rigid leather backing). Due to the numerous variables outlined, it is impractical to test all scenarios.
Computer modelling could dramatically reduce the amount of testing required. Models have identified mechanical degradation in lithium ion cells during cycling6 and have simulated lithium ion cells under abuse7. To our knowledge, there are limited open source publications modelling the effects of mechanical degradation on lithium polymer cells during realistic flexing scenarios.
A successful model may incorporate the following:
- Experimental observations as a basis to understand and then model particle-to-particle mechanical interactions in typical lithium polymer components, such as metal foils, coated electrodes and separators.
- Simulate the effect of the mechanical stresses that occur within a multiple layered lithium polymer cell during typical flexing in a wearable garment.
- Alter certain flexing variables (such as bending radii, etc.) to understand the effect of a variety of mechanical stresses on a lithium polymer cell.
- Consider the elastic properties of the substrate or material supporting the lithium polymer cell.
- Identify likely failure modes of a lithium polymer cell and when they may occur.
- Increase understandings of how the mechanical degradation effects the electrical response of a lithium polymer cell.
- Include the effect of stresses from flexing on interconnects and woven conductive fibers.
Modelling human biomechanical movements is out of scope of this project.
Example Approaches:
The unmounted soldier has an ever-increasing need for human portable power, leading to an increasingly heavy burden. It is desirable for equipment to be powered by light-weight lithium polymer batteries that are body-borne, garment embedded, conformal, not impacting movement, and distributed evenly across a soldier. However, a barrier to utilizing such a system is the unknown effect of the mechanical stress on the lithium polymer cells, and subsequent impact on safety and the electrical performance fatigue. For example, if a lithium polymer cell is embedded within the soldier’s garment, what are the effects of the mechanical stresses that the lithium polymer cell may undergo when the soldier is running?
Relevance to the Intelligence Community:
A successful project will be an enabler for energy systems based on lithium polymer cells across a body-borne garment, filling a technology gap, which is common to all wearable electronics industries. This could result in the use of a more conformal power source that does not impact the garment or comfort of the consumer compared to conventional rigid cased batteries. The model will enable fundamental understandings on the effect of the mechanical stresses on a lithium polymer cell, it will inform the safety case, and the reliability of any system which incorporates wearable lithium polymer cells.
References:
- Hayward, J. Chansin, G. Zervos, H. (2017, April). Wearable Technology 2017-2027: Markets, Players, Forecasts: IDTechEx. Retrieved from https://www.idtechex.com/en/research-report/wearable-technology-2017-2027-markets-players-forecasts/536
- Hayward, J. (2017, February 24). Textiles 2017-2027: Technologies, Markets, Players: IDTechEx. Retrieved from https://www.idtechex.com/en/research-report/e-textiles-2017-2027-technologies-markets-players/522.
- Ambrósio, J., Quental, C., Pilarczyk, B., Folgado, J., & Monteiro, J. (2011, May 27). Multibody biomechanical models of the upper limb. Retrieved from https://www.sciencedirect.com/science/article/pii/S2210983811000034.
- Thompson, W. K., Gallo, C.A., Crentsill, L. (2015, September 1). NASA Technical Reports Server (NTRS) - Digital Astronaut Project Biomechanical Models: Biomechanical Modeling of Squat, Single-Leg Squat and Heel Raise Exercises on the Hybrid Ultimate Lifting Kit (HULK).
- Stoppa M, Chiolerio A. (2014, July 7). Wearable Electronics and Smart Textiles: A Critical Review. Sensors. 2014; 14(7):11957-11992.
- Laresgoiti, I., Käbitz, S., Ecker, M. and Sauer, D. (2015, December 30). Modeling mechanical degradation in lithium ion batteries during cycling: Solid electrolyte interphase fracture. Journal of Power Sources. 300, 112-122.
- Ali, M.Y., Lai, W., Pan, J. (2015, January). Computational models for simulation of a lithium-ion battery module specimen under punch indentation. Journal of Power Sources. 273, 448-459.
Key Words: Battery, Batteries, Electrochemical Cells, Li-Ion, Lithium Polymer, Modelling, Mechanical Stress, Wearables, Wearable Applications, Composite Structures, Failure Modes, Conductive Textiles
Postdoc Eligibility
- U.S. citizens only
- Ph.D. in a relevant field must be completed before beginning the appointment and within five years of the application deadline
- Proposal must be associated with an accredited U.S. university, college, or U.S. government laboratory
- Eligible candidates may only receive one award from the IC Postdoctoral Research Fellowship Program
Research Advisor Eligibility
- Must be an employee of an accredited U.S. university, college or U.S. government laboratory
- Are not required to be U.S. citizens
- Citizenship: U.S. Citizen Only
- Degree: Doctoral Degree.
-
Discipline(s):
- Chemistry and Materials Sciences (12 )
- Communications and Graphics Design (2 )
- Computer, Information, and Data Sciences (16 )
- Earth and Geosciences (21 )
- Engineering (27 )
- Environmental and Marine Sciences (14 )
- Life Health and Medical Sciences (45 )
- Mathematics and Statistics (10 )
- Other Non-Science & Engineering (2 )
- Physics (16 )
- Science & Engineering-related (1 )
- Social and Behavioral Sciences (27 )


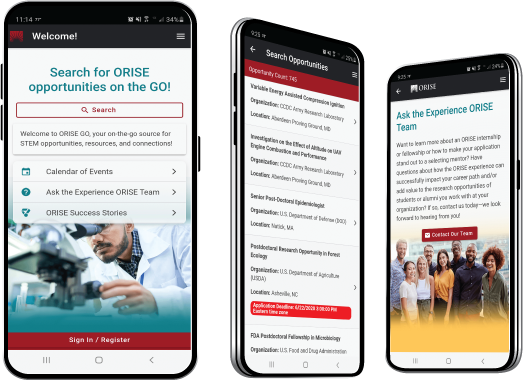
The ORISE GO mobile app helps you stay engaged, connected and informed during your ORISE experience – from application, to offer, through your appointment and even as an ORISE alum!